Lampin recently installed a brand-new Okuma Multus boring and milling machine, which is designed to optimize product quality and increase manufacturing capabilities. The Okuma Multus provides us with the ability to manufacture parts with a larger maximum material diameter in an efficient, one-step operation. With increased efficiency in-house, we can produce larger, more complex parts with the fastest lead times in the industry.
Senior Machining Specialist Richard Houle has been a dedicated employee-owner at Lampin for 32 years. He’s seen the technology of the manufacturing industry grow and change over the course of his career. With comprehensive on-the-job training and experience, Mr. Houle is able to adapt with the times and keep things moving smoothly as he operates the brand-new boring and milling machine.
One-Step Machining Streamlines Operations
The Okuma Multus is a boring machine that combines turning with vertical and horizontal milling. What are the benefits of having a machine that can perform multiple functions in one operation? According to Mr. Houle, the best benefit is the fact that parts are completed when they come off the machine and require no additional machining operations.
“There are a lot more chances of making a part defective with multiple machines. Handling the parts from machine to machine can cause dents, dings, or scratches,” said Mr. Houle.
Past machining processes required the use of many different machines to complete a single part. Between each stage, the part was removed and transported to its next operation by hand. This created ample opportunity for operator error and other mishaps that could damage the material before it was finished. The process also caused inevitable differences in tolerance, which caused issues when assembling very precise components. The one-step operation of the Okuma Multus guarantees clean, consistent results every time.
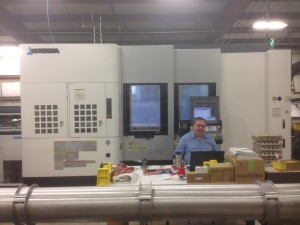
CAPTION: CNC machining expert Richard Houle works with Lampin’s new Okuma Multus boring and milling machine.
Comprehensive Knowledge Makes Adapting Easier
Adapting to the evolution of new technologies is an important aspect of the manufacturing industry. In the past, machinists were trained to perform one task on one machine so parts could be transferred between operations as quickly as possible. Now, cites Mr. Houle, the biggest challenge for a machinist is staying informed. With every operation combined into one step, the operator needs to be familiar with turning, milling, grinding, and CNC programming.
“We do our programming using software, which means you need to be trained in the use of the software as well as being trained on how to use the machine itself,” said Mr. Houle.
CNC Boring and Milling Accelerates Operations for Better Customer Service
Lampin’s machinists are kept up to date on all manufacturing processes, including the use of CNC software to run the machines. That’s why the introduction of a new machine is no trouble for the team on the manufacturing floor. Their experience and skills have allowed for a seamless transition as the efficiency and speed of the Okuma Multus improves Lampin’s manufacturing processes.
We’re eager to put the new machine through its paces. Contact the turning and milling experts at Lampin and get a quote on your component manufacturing within 24 hours!